The Untold Story on Aluminum Single Wire That It's Essential to Read o…
페이지 정보

본문
FIG. 30 exhibits a result of change in crystallization of the Al wiring because of a mechanical stress of the interlayer insulating film. FIG. 2 shows an example of temperature change with respect to time, in response to the first embodiment. FIG. 34 exhibits the easily curved surface of the higher floor of wring downwardly based on the seventh embodiment. Having good wettability signifies that materials is formed onto a layer or a groove in such a way that: a contact angle between, say, an upper material and a lower material disposed underneath the higher materials is comparatively low. K is a coefficient with regard to the surface tension .gamma..sub.B Of material B, and subscripts therefor show respective systems. Then, the floor tension (.gamma..sub.A), the interfacial tension between the fabric A and material B (.gamma..sub.AB), and the surface tension of fabric B (.gamma..sub.B) are balanced such that the following Young's equation holds. Then, a movie thickness of the SiO.sub.2 33 was 1.6 .mu.m. Therefore, it's fascinating that, within the course of forming a single-crystal wiring by uniform filling, the wettability shall be improved and the movie thickness of the wiring metallic shall be managed to a necessary minimum such that the quantity of the metallic is adequate to fill in the quantity of wiring groove.
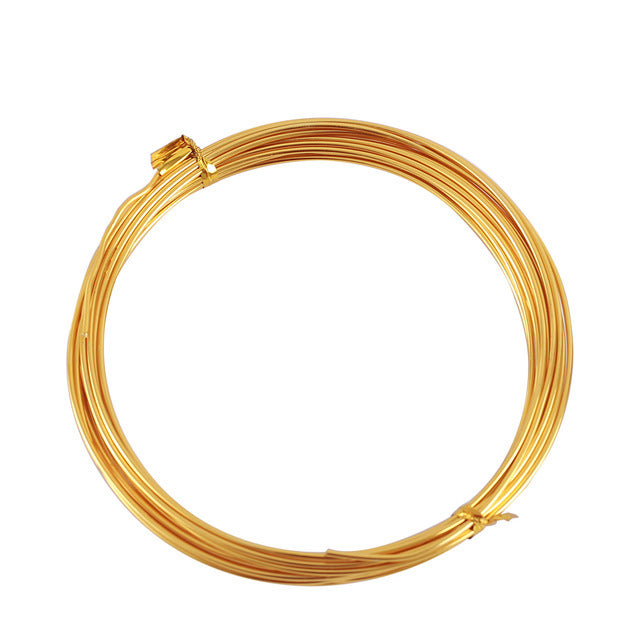
FIGS. 24A and 24B show cross sectional views showing that the steel skinny movie is agglomerated after the metal thin movie on the groove is selectively removed. FIG. 31 exhibits an instance of the electrode wiring structure the place the barrier metal is formed by the inside floor of the groove. FIG. 30 exhibits a results of difference in crystallization of the Al wiring as a consequence of a mechanical stress of the interlayer insulating movie noticed by the X-ray diffraction technique. Next, similar to the first embodiment again, the above device was annealed utilizing a halogen lamp heater from a back aspect of the substrate below the same vacuum background as in the sputtering for duration of 1 minute, as shown in FIG. 10C. In other phrases, the machine was in-situ annealed so that Al is crammed in the groove as a result of agglomeration. This makes the motor flip a technique or the opposite. There are 6 neurons, and 4 motors (a neuron for each path the entrance pair and rear pair of motors can flip. A diffracted X-ray is detected such that the X-ray incident angle is aligned to an angle in response to the Al route. FIG. 21 reveals a correlation between the contact angle of Al and C and the film thickness.
FIG. Three reveals relationship between thickness of Al film and a temperature at which an Al filling within the groove is feasible. With reference to FIG. 1A, a thermal oxide movie 12 whose thickness is approximately 1 .mu.m is formed on the Si substrate 11, and on the thermal oxide film 12 there is formed a wiring sample groove whose depth and width are approximately 0.02 .mu.m by 0.5 .mu.m and 0.5 .mu.m by means of 2 .mu.m, respectively, by a photo-lithography and a reactive ion etching (RIE). Then, Al with purity 99.9999% is used for a sputtering goal, and the Al thickness is made equal to depth of the groove such that Al is formed to the thickness of 0.02 .mu.m-0.5 .mu.m. Then, a combined fuel of CF.sub.4 and H.sub.2 was used and every gas of CF.sub.4 and H.sub.2 was provided at a circulation rate of 16 SCCM and 24 SCCM, respectively. FIG. Four exhibits relationship between a production price of a reaction product by an oxide movie as a substrate and Al, and temperature thereof, by way of logarithmic graph. 3.18.instances.10.sup.17 exp -(2.562/kT) and reveals relationship between the reaction charge and the temperature. FIG. 18 reveals that materials B on a flat materials A becomes orbicular form beneath a thermal equilibrium state.
FIGS. 19A and 19B present a system i the place the material B is agglomerated orbicularly on the substrate materials A having a groove therein and a system 2 the place the material B is crammed into the groove, respectively. When the fabric B on the flat materials A is agglomerated with annealing as described above, the fabric B kinds some spherical agglomerations. FIG. 9B shows a cross part of FIG. 9A where Al is stuffed into the contact or by way of hole by in-situ annealing. FIG. 23 exhibits a function profile the place there may be supplied a reflection preventing film such as C film and TiN film which are formed in the back side of the substrate by annealing. FIG. 35 exhibits an electrode wiring construction in response to the eighth embodiment. FIGS. 44A-44C present an electrode wiring construction where the wettability enhancing layer is formed within the inner floor of the groove. However, when the agglomeration is extended over the groove, the movie may be more stabilized if it is filled into the groove. It shall be appreciated that an arriving time within which the agglomeration doesn't happen further in the groove may be kept as such though in the expertise carried out by the candidates this time the device is cooled in a natural manner after a temperature rise.
- 이전글룰렛이벤트【GΟSU33·COM】777무료슬롯머신 24.12.28
- 다음글The Dirty Truth on Bob 24.12.28
댓글목록
등록된 댓글이 없습니다.